A Complete Guide to Printing Machines for Corrugated Packaging
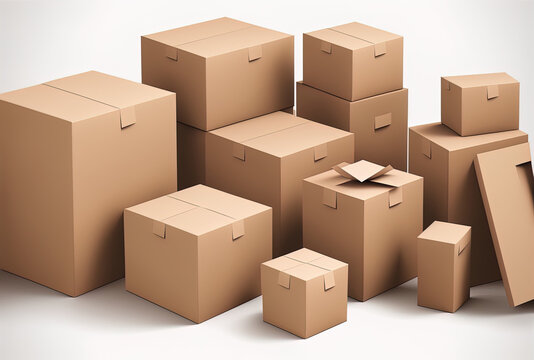
Corrugated packaging has become the most widely used material in e-commerce, logistics, and retail thanks to its strength, cost-efficiency, and sustainability. But the appearance and performance of corrugated boxes depend heavily on the printing machines used in production.
From simple one-color labels to high-resolution flexographic and digital printing on corrugated cartons, the right machine can significantly improve efficiency, reduce waste, and elevate packaging quality.
In this guide, you'll learn about the main types of corrugated printing machines—flexographic, digital, and offset— along with their benefits, applications, and selection tips for packaging manufacturers in 2025.
Why High-Quality Printing Machines Are Essential for Corrugated Packaging
In the world of corrugated packaging, appearance matters more than ever. Retailers expect neatly printed logos, barcodes, and designs. Customers notice the quality of packaging, and logistics demand clear, accurate identification. That's why investing in a reliable and precise printing machine is no longer optional—it's essential.
Key advantages of using modern printing machines include:
- High-speed performance for large production runs
- Precision print registration, even on recycled or textured board
- Reduced waste and downtime with automated setup systems
- Cost savings over time through better ink management and maintenance systems
Corrugated box producers now demand more from their machinery—not only in terms of print quality but also in how machines integrate with the full box production line.
Types of Printing Machines for Corrugated Packaging
Several printing methods are used in corrugated production. Each has its own strengths depending on your output volume, product type, and budget.
1. Flexographic Printing Machines
Flexographic printing is the most popular method for printing directly on corrugated board. It uses flexible printing plates, quick-drying inks, and high-speed roll-fed systems.
Benefits:
- Fast and efficient for large-volume runs
- Suitable for both simple and multi-color designs
- Works well on kraft and recycled liners
- In-line integration with die cutting, slotting, folding, and gluing units
Flexo presses offer versatility across various box sizes and styles, making them a backbone for packaging facilities.
As a reliable flexo printing machine supplier, Gaint offers durable, high-precision systems built to meet the needs of modern corrugated packaging plants. Our solutions are used in factories that prioritize speed, accuracy, and reliability.
2. Digital Printing Machines
Digital printing has grown in popularity, especially for short runs and customized designs. Instead of using plates, digital machines print directly from a computer file, allowing for quick changeovers.
Ideal for:
- Personalized packaging
- Prototyping or low-volume production
- Jobs requiring variable data printing (e.g. QR codes, barcodes)
While digital printing allows for more flexibility and design variety, it's generally slower and more expensive than flexographic systems for high-volume runs.
3. Offset Printing (Laminated Sheets)
Offset printing is often used for high-end packaging applications. It provides photographic quality but is usually done on sheets that are later laminated onto corrugated board.
Use Cases:
- Premium product packaging
- Retail-ready displays
- Promotional boxes with detailed graphics
Due to higher costs and slower throughput, offset printing is not common in mass-market box production.
Integrated Corrugated Printing and Converting Machines
Modern packaging operations benefit from machines that go beyond simple printing. These integrated systems combine multiple functions to streamline production and reduce manual handling.
Flexo Printer Slotter Die Cutter & Folder Gluer/Stitcher Counter Ejector
This type of all-in-one system is designed to handle:
- Flexo printing
- Slotting and die cutting
- Folding and gluing
- Stitching and counting
With this configuration, raw board can be transformed into printed, finished boxes in one seamless process. It reduces setup time, minimizes floor space, and ensures consistent quality.
Automatic Folder Gluer / Stitcher Counter Ejector
These machines specialize in the post-print stage, handling folding, gluing or stitching, and counting. They're ideal for facilities looking to scale up output without adding labor.
Such equipment can be used as a stand-alone solution or in conjunction with printing and die-cutting units for a fully automated production line.
How to Select the Best Corrugated Printing Machine
Selecting the best machine depends on several production-related factors. Here are key aspects to evaluate before making a decision:
1. Box Design and Complexity
Do your boxes have simple text or full-color images? Do they require complex die cuts?
2. Print Volume
High-speed flexo machines are ideal for continuous large-volume orders, while digital is more suitable for lower runs and frequent changeovers.
3. Substrate Quality
Recycled kraft liners can be challenging to print on. Your choice of ink and print pressure must suit the surface texture and absorption level.
4. Required Integration
Do you want your machine to also perform die cutting, folding, gluing, or stitching? Integrated systems can save time and labor.
5. Operator Skill and Maintenance
Machines should be easy to use, maintain, and troubleshoot. Remote diagnostics and local service support are added advantages.
By working with experienced equipment suppliers, you can get valuable insights during the selection process. Manufacturers who understand the challenges of corrugated packaging—like Gaint—can offer tailored solutions, training, and after-sales support.
Key Benefits of Modern Flexo Printing Machines
Upgrading to a modern printing system is not just about speed; it's also about improving process efficiency and output quality.
Here's what advanced machines typically offer:
- Servo-controlled accuracy for clean print registration
- Quick setup features that minimize downtime
- Low waste rates, helping to reduce production costs
- Inline automation to streamline box manufacturing
- Modular design, allowing for future upgrades
By investing in machines that meet both current and future needs, packaging companies can remain competitive and agile in changing markets.
Corrugated Printing Machine Trends in 2025
As demand for sustainable and visually appealing packaging continues to grow, several trends are shaping the future of printing machines:
- Eco-friendly ink formulations (e.g. water-based and biodegradable inks)
- Smaller batch production driven by e-commerce and personalization
- Smarter machines with AI-based diagnostics and predictive maintenance
- Energy-efficient systems that reduce environmental impact
- Full-line automation with seamless integration between modules
Printing equipment is evolving rapidly, and staying ahead of these trends can help packaging companies gain a significant market advantage.
Frequently Asked Questions (FAQ)
1. What is the most common printing method for corrugated boxes?
Flexographic printing is the most widely used method due to its speed, versatility, and cost-effectiveness.
2. Is digital printing suitable for corrugated packaging?
Yes, digital printing is ideal for short runs, prototypes, and customized packaging, though it's less efficient for mass production compared to flexo.
3. What printing method should I choose for premium packaging?
Offset printing with laminated sheets is preferred for retail displays and high-end packaging requiring photo-quality graphics.
4. How much does a corrugated printing machine cost?
Basic flexo printers can start at $50,000–$100,000, while fully automated lines may reach several hundred thousand dollars.
5. Which supplier offers reliable corrugated printing machines?
Giant provides flexo, digital, and integrated solutions, known for durability, precision, and global after-sales support.
Conclusion: Investing in the Right Corrugated Printing Machine
Choosing the right printing machine for corrugated packaging is a strategic decision that can influence every aspect of your production—from cost and speed to quality and flexibility. Whether you're investing in a high-speed flexo printer slotter or upgrading to an integrated converting system, the goal is the same: better efficiency, consistency, and output.
With years of experience in the industry, Gaint supports corrugated box manufacturers by offering dependable, customizable printing and converting solutions. Our machines are built with performance and durability in mind, helping clients optimize production lines and meet growing market demands.